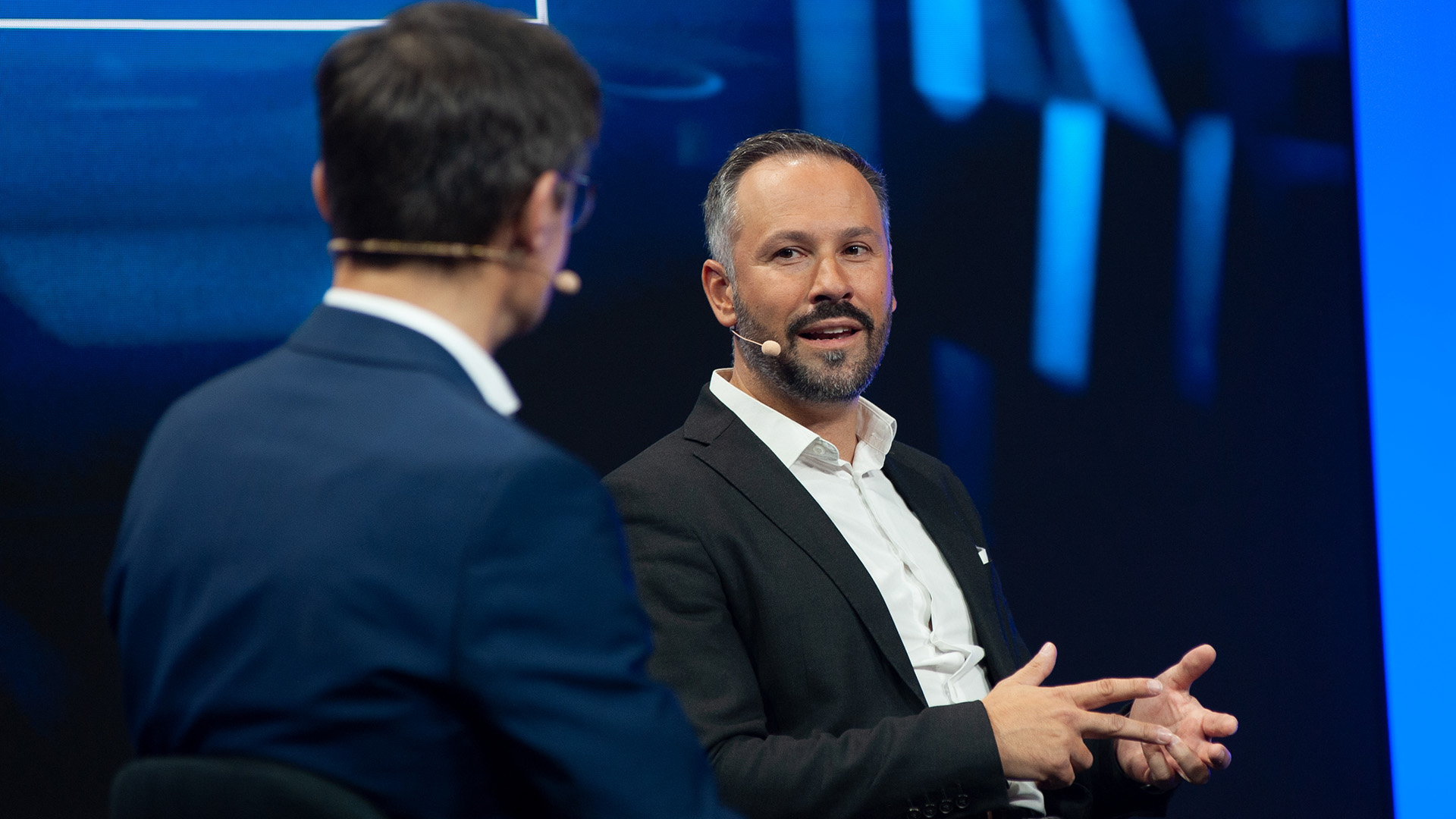
Quid Pro Quo Of A Special Kind
RSGetriebe Expands Production With Palloid And GearSKIVING Processes
One wheel meshes with the other - it is impossible to imagine the state-of-the-art machinery of RSGetriebe in Sonthofen without the high-quality complete turning/milling machining centers fromDMG MORIAs a manufacturer of special gearboxes and customized drive concepts, RSGetriebe in Sonthofen has been developing drive systems that set standards worldwide for more than 50 years. Thanks to the cooperation and physical proximity with the milling machine and lathe manufacturer DMG MORI, sophisticated gearMILL (cyclo-palloid) and gearSKIVING processes can be used for the rough and finish milling of various gears in gearbox production. During the two-week Open House at DMG Mori's Pfronten location, RSGetriebe Plant Manager, Ercan Senoldu, answered questions during a Technology Talk focusing on gear milling and explained the advantages of the newly added milling processes for our customers.
Mr. Senoldu, how exactly would you describe the cooperation between DMG MORI and RSGetriebe?
Senoldu: "The best way to see us is as a customer and partner alike. Thanks to the machines from DMG, we are able to use our turning-milling machines for cyclo-palloid gears and gears and splines in addition to our gear cutting machines (gear milling and shaping). They are therefore the perfect complement to ensure our high standards in the production of our gearbox solutions. By retrofitting the machines with the appropriate software, we can also guarantee our customers a wide spectrum in parts production at all times."
How should one envision the software update and the interaction with the machines?
Senoldu: "The principle of cyclo-palloid gearing is based on two eccentrically arranged cutter head groups, which have radii of curvature of different sizes. Normally, in the gear manufacturing milling process, the module is straight. However, in both cyclo-palloid and palloid milling operations, the tool must mill helical gears. For this to be successful, the module must have a certain inclination in order to be able to mill gears for so-called helical or spiral bevel gears. Such milling operations are performed at RSG on the DMU80 FD. Thanks to the GearMill software, in addition to all common types of gears, we can set the appropriate inclination angle for the palloid milling operation so that the operation can be carried out, taking into account the appropriate tools for the milling process in question."
What exactly does gearSKIVING mean?
Senoldu: „With gear skiving, a combination of gear hobbing and gear shaping, gears can be produced in series on turning/milling centers with the highest productivity and quality. Here, too, we have had the machine retrofitted with the appropriate software so that we can drastically minimize the idle times of our parts. In addition, we don't have to outsource production, but can manufacture all gear parts in-house without having to rely on an external supplier."
The HerkulesGroup has been working with DMG MORI machines at its various locations for years, for example with the CTX TC series complete turning/milling machining center for machining complex workpieces. The machines are also part of the state-of-the-art machinery in Sonthofen to ensure the required quality grades of the special gearboxes and drive elements.
You can find the complete interview (in German language only) as a video on DMG MORI's Youtube channel under the following link: DMG MORI Technology Talk - Gear Cutting (DE)
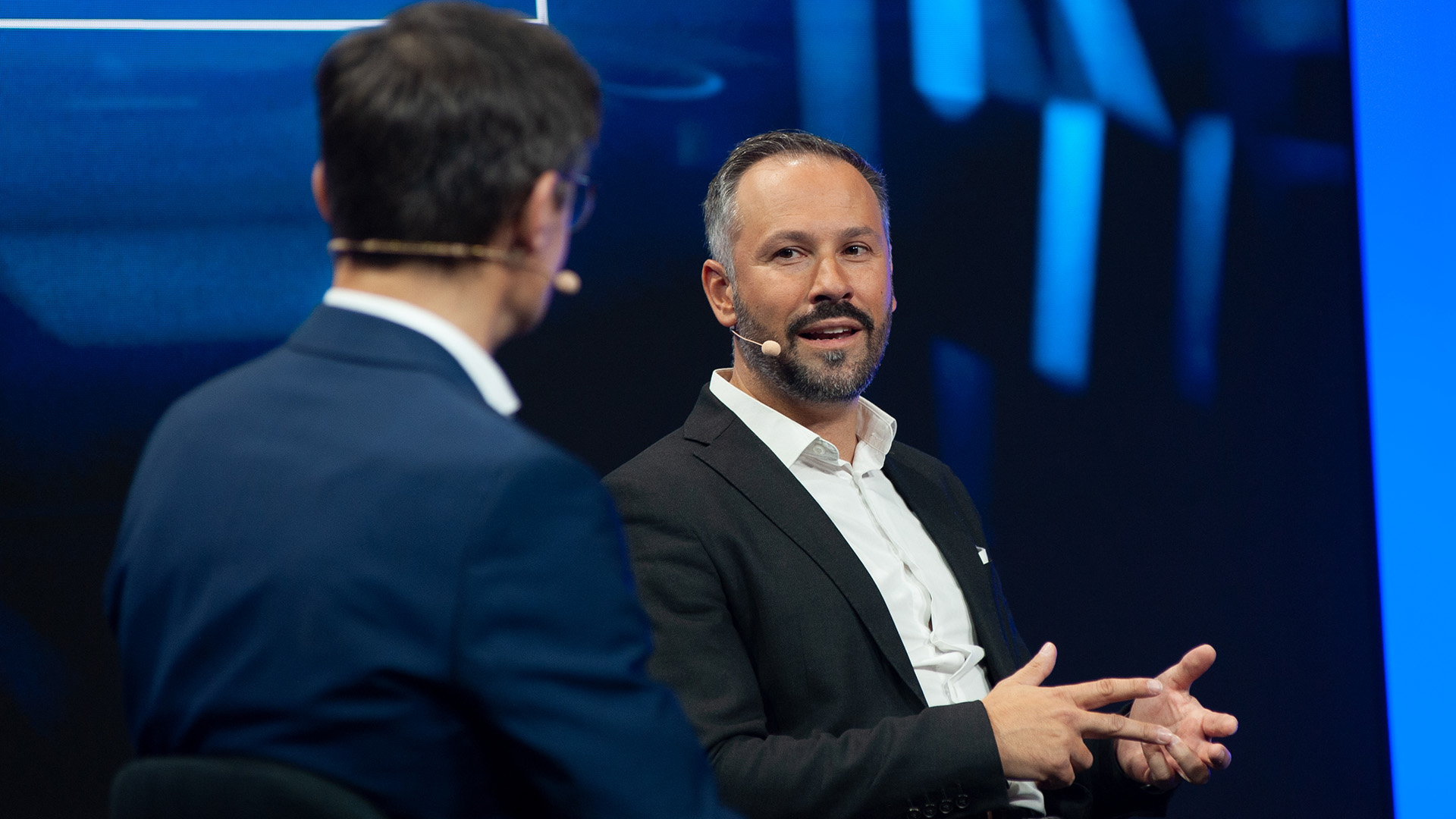
Quid Pro Quo Of A Special Kind
RSGetriebe Expands Production With Palloid And GearSKIVING Processes
One wheel meshes with the other - it is impossible to imagine the state-of-the-art machinery of RSGetriebe in Sonthofen without the high-quality complete turning/milling machining centers fromDMG MORIAs a manufacturer of special gearboxes and customized drive concepts, RSGetriebe in Sonthofen has been developing drive systems that set standards worldwide for more than 50 years. Thanks to the cooperation and physical proximity with the milling machine and lathe manufacturer DMG MORI, sophisticated gearMILL (cyclo-palloid) and gearSKIVING processes can be used for the rough and finish milling of various gears in gearbox production. During the two-week Open House at DMG Mori's Pfronten location, RSGetriebe Plant Manager, Ercan Senoldu, answered questions during a Technology Talk focusing on gear milling and explained the advantages of the newly added milling processes for our customers.
Mr. Senoldu, how exactly would you describe the cooperation between DMG MORI and RSGetriebe?
Senoldu: "The best way to see us is as a customer and partner alike. Thanks to the machines from DMG, we are able to use our turning-milling machines for cyclo-palloid gears and gears and splines in addition to our gear cutting machines (gear milling and shaping). They are therefore the perfect complement to ensure our high standards in the production of our gearbox solutions. By retrofitting the machines with the appropriate software, we can also guarantee our customers a wide spectrum in parts production at all times."
How should one envision the software update and the interaction with the machines?
Senoldu: "The principle of cyclo-palloid gearing is based on two eccentrically arranged cutter head groups, which have radii of curvature of different sizes. Normally, in the gear manufacturing milling process, the module is straight. However, in both cyclo-palloid and palloid milling operations, the tool must mill helical gears. For this to be successful, the module must have a certain inclination in order to be able to mill gears for so-called helical or spiral bevel gears. Such milling operations are performed at RSG on the DMU80 FD. Thanks to the GearMill software, in addition to all common types of gears, we can set the appropriate inclination angle for the palloid milling operation so that the operation can be carried out, taking into account the appropriate tools for the milling process in question."
What exactly does gearSKIVING mean?
Senoldu: „With gear skiving, a combination of gear hobbing and gear shaping, gears can be produced in series on turning/milling centers with the highest productivity and quality. Here, too, we have had the machine retrofitted with the appropriate software so that we can drastically minimize the idle times of our parts. In addition, we don't have to outsource production, but can manufacture all gear parts in-house without having to rely on an external supplier."
The HerkulesGroup has been working with DMG MORI machines at its various locations for years, for example with the CTX TC series complete turning/milling machining center for machining complex workpieces. The machines are also part of the state-of-the-art machinery in Sonthofen to ensure the required quality grades of the special gearboxes and drive elements.
You can find the complete interview (in German language only) as a video on DMG MORI's Youtube channel under the following link: DMG MORI Technology Talk - Gear Cutting (DE)