RSGetriebe
Your Partner for Customized Drive Solutions
As a specialist for custom gearboxes, RSGetriebe has been developing customized drive systems for over a half a century – and they have been setting standards throughout the industry for as long. The gearbox experts from Sonthofen find the correct solution for every industry sector and application.
Quality in every detail - to ensure the high quality of our gearboxes, we manufacture them exclusively to the highest quality standards. From the material cut to the gear wheel, all gear components pass through our ISO 9001:2008-certified production facility. Modern machinery and absolute care during assembly are further building blocks for the high quality “made in Sonthofen”.
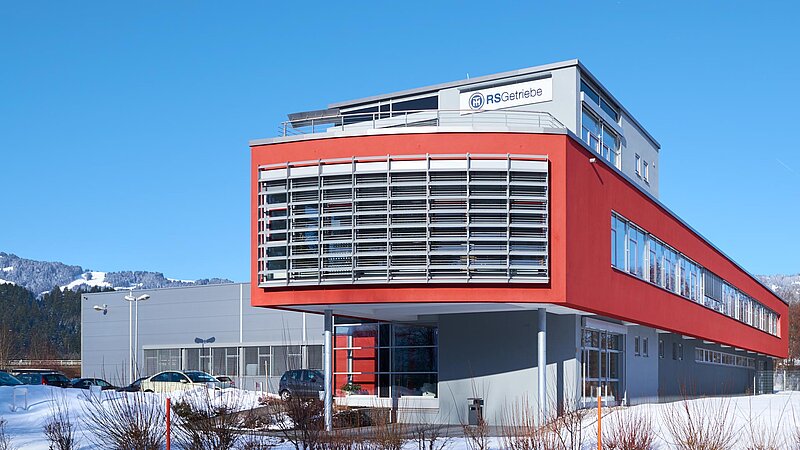
History
75 Years of Tradition in Gearbox Manufacture
The origins of gearbox manufacture go back to the year 1949, when the company Riedel AG begins with the manufacture of the light motorcycle Imme R 100 in Immenstadt under the leadership of the company founder Norbert Riedel. From 1956 on, some seven years and approximately 12,000 produced Immes later, the company decides to concentrate solely on the development and manufacture of gearboxes and the manufacture of motors and spare parts for the Immes is discontinued.
Find out more about the